Last updated on March 4th, 2022 at 01:45 pm
Increasing productivity while reducing costs and reducing risks is imperative in every industry. Industry 4.0 can help enormously here.
With industrial automation and the evolution of Industry 4.0 or IIOT, factories have a faster time to market, are more effective, and are more reliable, thereby reducing production costs. Embracing the Internet of Things in automation, Epsum Labs is engaged in the Internet of Things concept. We present our experiences using IoT in the manufacturing industry.
As part of our work, we worked with a chemical manufacturer that manufactures moisture-absorbing powder for steel, iron, aluminum, and power industries, that absorbs the excess dampness from the primal matter when sprayed onto it using a dosing machine. Initially, a machinist operated the dosing machine while the raw materials advanced via conveyer belt. A sample of the untreated raw materials is sent to a lab to determine its moisture content. The problem with this system was that there was no real-time mechanism based on which the dosing machine setpoint could synchronize since there was a latency in lab report generation.

During this timeframe, there was no analytics to determine if the correct amount of powder had been sprayed by the dosing machine on the primal matter moving on the conveyer belt or if it was excessive or low in quantity. That leads to waste, unneeded expenses, or substandard products if moisture is present in the primal material. To avoid this improper usage of moisture-absorbing powder, we at Epsum Labs designed an IIOT solution for the unit. To begin with, we installed cameras that captured images of the primordial material at different times. We then used advanced algorithms to build a model which could determine the amount of moisture in the primordial matter thus analyzing and predicting the quality and texture of the primordial material found in those images. After analyzing the images captured by the cameras, we installed an industrial gateway that transmits images to a server captured by an IP camera and receives predicted moisture content as a response. Based on the prediction values, it commands a dosing machine PLC with a dosing setpoint. That provided a real-time mechanism for the dosing machine to spray an adequate amount of moisture-absorbing powder based on the data collected from the images of the primal matter regarding its quality and the quantity of moisture it contained. That helped in loss curbing due to improper dosing in the plant.
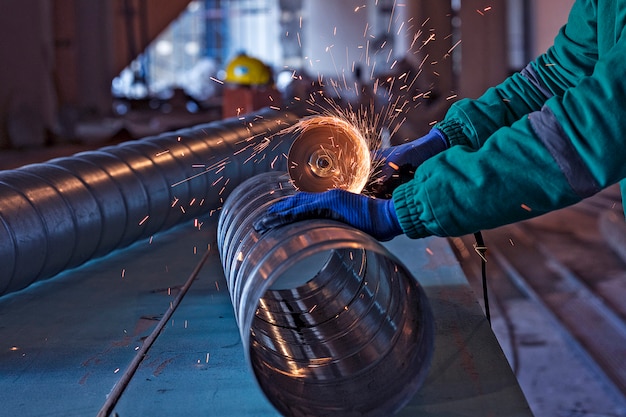
A web application was also built so that images and data from the automated process could be visualized, enabling the operations team to gauge the quality of primal matter and adjust the set point of the dozing machine manually based on the understanding of the matter.